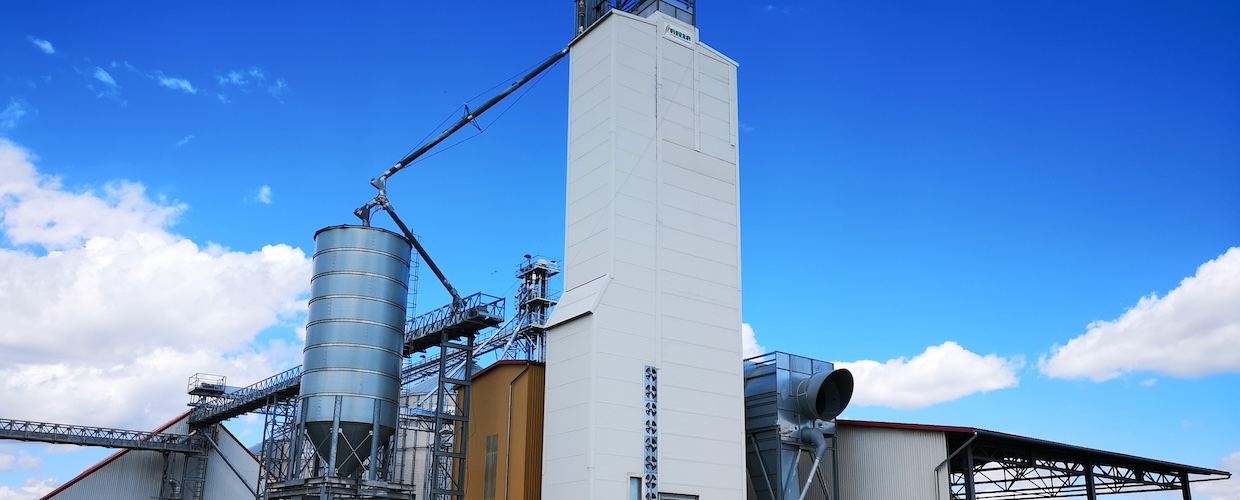
Crop drying is the final operation in crop production, without which most of our crops would be ruined in a few days. Its purpose is to slow down the physiological processes taking place in the grain so that it can be stored without damage, from the time of harvest to the time of use. It’s important to see precision farming as a complex, continuous process – one that does not end with the harvest. An essential part of this process at KITE is precision crop drying based on an innovative system that improves the safety and efficiency of grain dryers and that ensures a precision solution for the entire crop production process – in short, Videokontroll.
Crop drying today is a key issue - one that combines technical, technological, and economic challenges. Optimizing a dryer and the drying process itself is a highly complex task.
Videokontroll provides a solution for remote monitoring in respect of gravity-system cross-flow shaft dryers, which was developed in order to increase operational safety, energy efficiency and storage safety. The system helps to optimize the operation of the grain dryers and to prevent dryer fires. This results in healthier food and feed, as well as reduced energy costs and environmental pressures.
The system is suitable for the protection of Bábolna, Petkus, Stela, Riela, KWA, Bonfanti, Cimbria, Mikrotherm, Neuero and Tornum drying towers, among others, with up to several hundred measuring points, depending on the number of exit openings on the tower.
For safer drying!
Crop drying is a fire-hazardous process, but it can be controlled!
Working principle: The equipment measures the temperature of the hot air passing through the crop mass over the entire surface at the moment of exit, thus allowing the drying process to be monitored.
Each exit window of the dryer is equipped with a temperature sensor, providing site-specific temperature information for the entire tower in the form of a heat map.

A background based on modern information technology allows the technical correction of any deviations detected in the drying process. The corrections result in significant savings in tangible numbers compared to the previous operating state.
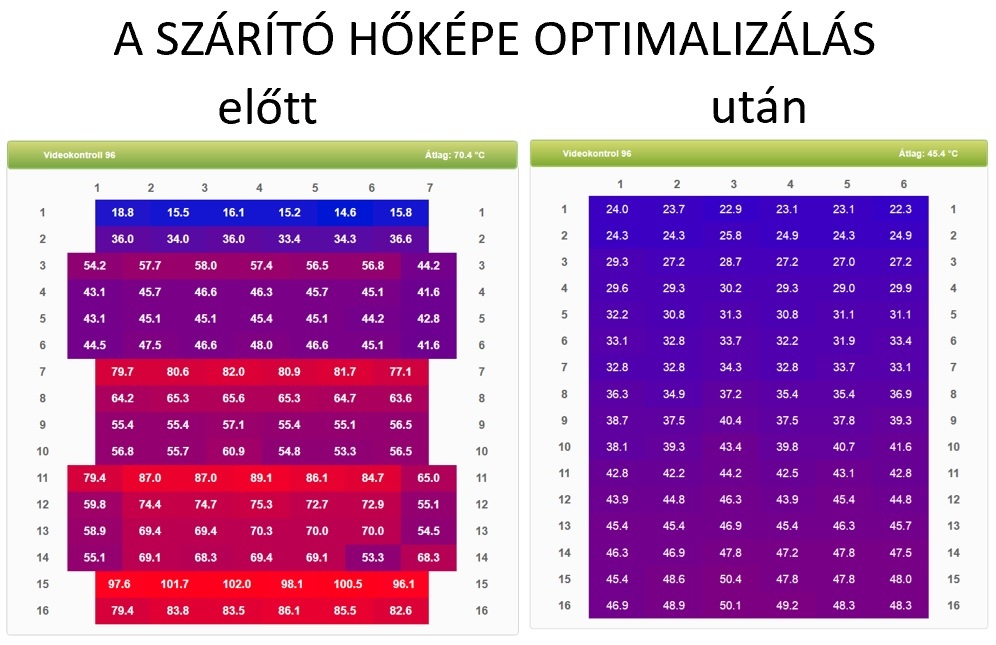
The system can also be retrofitted into cross-flow dryers, and all important parameters of the drying process can be followed on a monitor. What’s more, the owner can even monitor the processes taking place under the enclosure of a modern dryer using a mobile app.
Benefits:
- Fires from local blockages, overheating or spontaneous combustion can be prevented.
- It is proven to be well capable of detecting operational errors that cause uneven drying.
- By using the most advanced computer technology available, any jammed crop is indicated within a short time, long before a fire starts, and so the operator can intervene before damage occurs.
- As a result of tight control of the process, over drying can be avoided, which results in energy savings and an improvement in the nutritional value of the crop, while also improving the storability of the crop.
- The data measured by all sensors can be followed simultaneously on the monitor.
- It helps operators to perform the task to a high standard.
Through this optimization of the drying process, energy consumption is lower, environmental impact is lower, quality is better and profit is higher!
Our related services
- Dryer monitoring system design tailored to the dryer
- Dryer monitoring system installation
- Dryer optimization recommendation
- Dryer optimization implementation